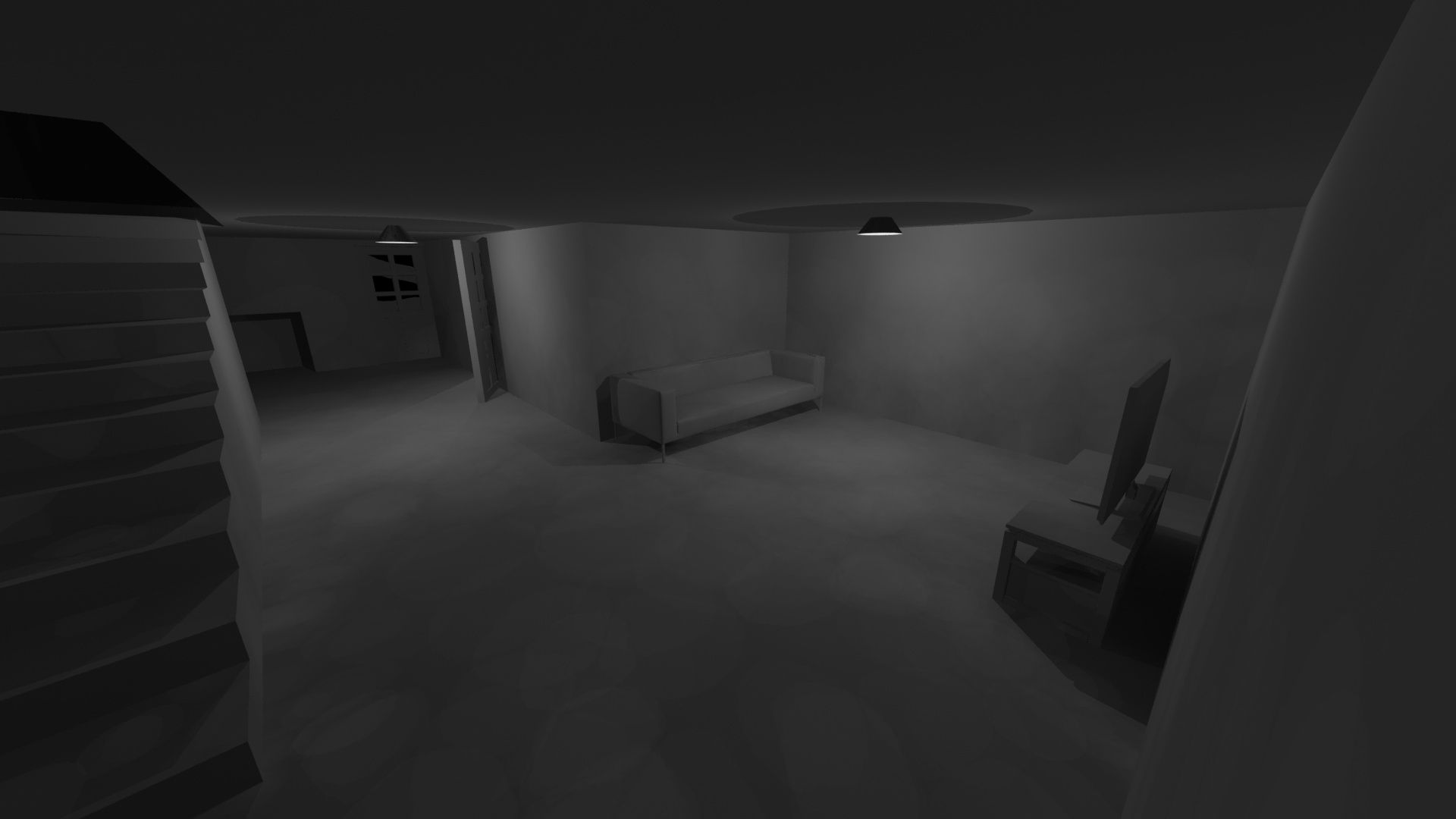
Unit 80/18
Work Experience
Introduction
Aim
This unit provides you with an opportunity to apply their knowledge, skills and understanding in the workplace and gain credit for working in a relevant area of the creative media sector.
Unit abstract
This unit is designed to develop your abilities to identify appropriate work placement opportunities in the creative media sector and explore the process of securing such placements.
Learners will develop both vocational and transferable skills within a practical industrial context.
Monitoring and evaluating the learner’s performance and learning experience is integral to this unit.
Learning outcomes
On successful completion of this unit a learner will:
-
Be able to identify and negotiate work experience placements in the creative media sector
-
Understand the requirements of negotiated work placements
-
Be able to undertake work experience placements as negotiated
-
Be able to monitor and evaluate own performance and learning during work placements in the creative media sector.
For work experience we've been asked to make a 3D model of a piece of military equipment. This is something we've done before with different equipment for the M.O.D. as the college has a connection with them.
We are splitting the workload between several of us, each making separate pieces of the model and having one of us put all of the pieces together. While making the model we have be very aware of how we build each piece because the client expressed the need for it to be 3D printable. This presents a few issues when it comes to modelling. Not only do each of the pieces need to be made in a very specific way to allow the 3d printer to actually print them, but also each piece needs to be able to slot together in such a way that either snaps in to place or can be glued.
After several parts had been chosen I decided to create the 2 Ports/Caps on the back of the equipment, this was mainly down to the interesting shape of the larger cap. The 2 images below are the only references I had to work with which present a couple of issues due to lack of detail and different angles. As you can see there is almost nothing the work off for the smaller, blue port as it's blocked by a strap. There's also no pictures of inside either the ports or the caps.
Through the process of creating these models I have been putting a focus on using the optimal amount of polygons, this helps the project in multiple ways. The main reasons I am focusing on Poly-count are firstly, good practice, as I plan on creating models for video-games too many polygons in a scene will make the game run much slower. Secondly, as this model is being designed to 3D printing an excess of polys can confuse the 3D printed making the model break during printing.
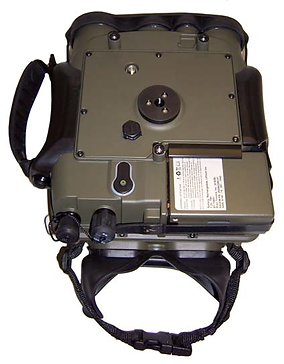



Once every piece had been modelled, Scott put the pieces together in the most logical way, by slightly resizing a lot of the components he was able to very cleanly fit each section onto the main body of the piece. This work especially well seeing as Scott's chosen section was the Main body of it so he knew the ideal places to be slightly edited for a clean fitment.
Although I'd say this project went smoothly on my end the main issue was the amount of workload that was stacked on Scott to finish the piece, all while using a varying quality of 3D models as some of the participants were very new to modelling. This meant that Scott had the task of fixing some models to work with the main product before attaching them, which was yet more time spent later in the project that we could have saved earlier by ensuring everyone knew some fairly simple modelling rules beforehand.
Comments:
Emilio: "high level of team work and technical skills have been employed in the creation of this project. The final submission to the client met with much enthusiasm and the 3d Printing can now take place due to the excellent topology and structural form of the model. Congratulations Team."